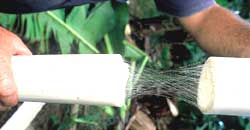
If someone is questioned about the raw material used to make paper, the instant answer is wood. Those who know a little more about the papermaking process would mention agricultural waste and recycled paper. Ironically, no one would talk about banana fibre or coconut shells, raw materials that can make the paper industry sustainable in the long run.
The trend of using banana fibre to manufacture handmade paper is now picking up, especially in developing nations like India. The development is noteworthy, as banana paper can be 300 times stronger than the normal paper. While paper from woodpulp has a bursting force (unit to measure paper strength) in the range of 15-20 units, banana paper's strength is as high as 44 bursting force.
The use of the fibre can also solve a problem: disposal of the plant's trunk. The plant bears fruit once in its lifetime; after harvesting, most of it is nothing more than waste. Thus, it needs to be disposed of -- a mammoth problem in India, the world's largest producer of bananas. In 2003, the country produced about 16.5 million tonnes of the fruit.
Some artisans use the fibre to make ropes, handbags,
sarees and a variety of handicraft items. But banana papermaking seems to be the only avenue for utilising this resource most appropriately. If all the banana plants were harvested and their fibre extracted from the trunk, around 2.1 lakh tonnes of the fibre would be available per annum, yielding 1.65 lakh tonnes of handmade paper. Bearing in mind that India's production of handmade was estimated to be a mere 27,000 tonnes in 2002-03, with the main raw material being cotton rags, this figure is staggering.
Slowly unpeeling the wonder Following recent research by the Jaipur-based Kumarappa National Handmade Paper Institute and the Dehradun-based Forest Research Institute, some entrepreneurs have become aware of the economic value of the fibre. Kerala, Tamil Nadu and Andhra Pradesh are slowly becoming the hubs of commercial extraction, providing work to many unemployed youth and women. "Since banana fibre extraction has a significant employment generation potential, we have started conducting training workshops in other states like Maharasthra (the banana belt) and Bihar," reveals R Rajan, deputy director, Handmade Paper Industry, Khadi Villages and Industries Commission (
kvic), Mumbai.
There are two ways of extracting the fibre: manual and mechanical. The former involves cutting the trunks into small pieces and scraping them with the help of a comb-like structure called the scraper. An individual can scrape around 0.8 to one kilogramme (kg) of fibre in eight hours. Mechanically, around 10-12 kg of the fibre can be extracted in the same duration. But the quality of the manually extracted fibre is far better, as it has low levels of pith and moisture. This is the reason it fetches a higher price (Rs 80-85 per kg) than the mechanically extracted fibre (Rs 60-65 per kg). Moreover, manual extraction of the fibre from all the banana trees of the country can create as many as 5.6 lakh jobs per year, whereas mechanical extraction would provide employment to only 47,000 people.
In most of the fibre-extraction centres, villagers are directly linked with suppliers (middlepersons) rather than the paper manufacturers. The suppliers have developed a network of farmers; for instance, Shivkumar, based in the Rajahmundry district of Andhra Pradesh, has a network of 50 villagers who provide him with 300 kg of the fibre per month. "I supply most of this fibre to Jaipur, as the majority of handmade paper manufacturers are based there," says Shivkumar. In some places, non-governmental organisations like the Vivekanand Pratisthan of Maharastra and self-help groups are involved in the fibre collection/supply process, ensuring a fair price to the villagers.
Some paper manufacturers producing banana paper on a continuous basis prefer to have their own supply network, as it proves to be cost-effective. One such manufacturer is Ram Avtar of Jaipur-based Shivam Paper -- one of the country's leading producers of banana paper.
Paper profits The banana paper industry can attract many more enterprising people like Avtar because it is extremely rewarding. Though the total cost of manufacturing banana paper is as high as Rs 200 per kg, a manufacturer often has a profit margin of Rs 200-220 per kg, with the handmade paper selling at Rs 400-420 per kg. The paper's value-added products such as gift wrappers, envelopes and stationery items fetch much higher prices. For example, a lantern made from the paper costs as much as Rs 100.
The only drawback is the niche market. The majority of the paper is exported, that too in the form of value-added products, to countries such as Germany, the
us and France. "The domestic demand is very low. Consequently, most manufacturers prefer to produce banana paper only when they get orders," says M Bhoomiah, assistant director, Handmade Paper Industry,
kvic. If the government subsidies the value-added products or the paper itself, a domestic market could be created. The industry would then flourish and employment would be generated for many more. "The need of the day is to forcefully market the ecofriendly prod uct. Else, an extremely useful resource would always be 'considered' as a waste," concludes Sheshagiri Rao of the Handmade Paper Industries Association, Andhra Pradesh.