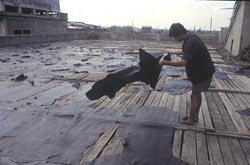
In clearing the tenth five-year plan recently, the Union cabinet gave the green light to a programme that seeks to metamorphose the leather industry into an environment-friendly sector. While the tanning process will no longer cause pollution, leather itself would become a completely biodegradable product if this plan is successfully implemented.
"The main objective is to make a paradigm shift from chemical processing to bioprocessing," reveals T Ramasami, director, Central Leather Research Institute (
clri), the national apex research body for leather and related products, and a Council of Scientific and Industrial Research (
csir) affiliate. The programme would involve 11 institutions -- eight of them outside the
csir umbrella. "It is one of the components of the tenth plan under the national environmental mission for the tannery sector," adds Ramasami (see box: Bullish on leather ).
"Given the contribution this sector makes to the country's economy it cannot be ignored. A clean-up operation was, therefore, the need of the hour," avers Paul P Appasamy, director, Madras School of Economics, Chennai.
Jekyll and Hyde Even as leather exports worth upwards of Rs 6,800 crore took place in 1999-2000, the target for 2002 is Rs 10,000 crore. On the domestic front, too, the industry makes a significant contribution. It comprises over 3000 tanners and employs more than 1.5 million people. The hubs of leather production in the country are Vellore and other cities in Tamil Nadu (60 per cent), Kolkata in West Bengal (15 per cent), Kanpur in Uttar Pradesh (12 per cent) and Jalandhar in Punjab (5 per cent), points out A Sahasranaman. He is the programme coordinator, United Nations Industrial Development Organisation (
unido). "The catch is that while processing about 2500-3000 tonnes of raw material, Indian leather units generate nearly 80,000-90,000 cubic metres of wastewater per day," adds Sahasranaman.
"The leather industry in India as well as in other developing countries has caused serious damage to the local ecology," informs Appasamy. Due to strict enforcement of environmental norms in industrialised nations during the past few decades, tanning operations gradually shifted to developing countries like India. The leather industry boomed here since green laws had no teeth.
As the volume of trade increased, faster processes were adopted. Traditional and ecofriendly raw materials such as vegetable tans suddenly gave way to chemical inputs like chromium. Not only did the latter expedite the tanning process, they also delivered a better quality product. These benefits, however, came at a steep environmental cost.
Chemicals became the main cause of pollution from tanneries. Sample this: the tanning of one kilogramme (kg) of leather requires about 35-40 litres of water, all of which is polluted during various processes of converting skin into leather. For decades now this wastewater has been discharged without any kind of treatment. Consequently, local waterbodies located near tanneries have been severely polluted.
"In Tamil Nadu (
tn), wastewater from tanneries has seeped into the local sources of irrigation affecting an area of 35,000 hectares," says S Janakarajan, professor, Madras Institute of Development Studies, Chennai. "Even common effluent treatment plants (
cetps) have failed to address the problem in its entirety," he feels. "In this regard, compliance with total dissolved solids (
tds) norms remains a major parameter for which no satisfactory solution has been found yet -- not only in India but elsewhere in the world too," reveals Sahasranaman.
Solid waste, mostly fleshings, has often been dumped in the open contaminating both surface water and groundwater. This has also spawned unhygienic conditions in the area.
Expectedly, the industry has been under the scanner because of its highly polluting nature. In recent times, there have been a slew of court directives asking tanners to either shape up or ship out (see box: Action and reaction). The Indian industry has also had to face cut-throat competition from foreign players, particularly leather exporting units located in the Southeast Asian region. And the complex new global economic order has queered the pitch further. In the face of the triple whammy, the domestic segment can only survive by opting for cleaner technologies and benchmarking itself against the international leather industry.
Banking on biotech It is against this backdrop that the Union government has decided to step in with its ambitious programme under the tenth plan.
Step I = Abattoir waste is mixed with sludge and other material
Step II = Waste is minced before being transferred to the biodigester
Step III = Anaerobic soil bacteria break down the waste resulting in production of biogas
Step IV = After the retention time of 28 days waste is sent to the buffer tank and later sold as nutrient-rich manure
Step V = Gas is stored in a balloon and used to generate power
Source: Anon 2002, Report on 60 mt biomethanation plant to generate power from solid waste of Al-Kabeer Exports Pvt Ltd, Central Leather Research Institute, Chennai, mimeo Though the roadmap is still at the drawing board stage, it is quite evident that biotechnological breakthroughs will form the bedrock of the programme. Closely linked to it are
clri's successful experiments with biomethanation plants.
The project on the 'Development of High Rate Biomethanation Processes as means of Reducing Greenhouse Gases Emission' commenced in September 1994 for a duration of five years. It had an outlay of Rs 40 crore out of which Rs 15.80 crore was provided by the Global Environmental Facility (
gef). The Union ministry of non-conventional energy sources (
mnes) had to give
Rs 14.20 crore and the remaining cost of about Rs 10 crore was to be borne by beneficiary organisations.
The biomethanation project is being implemented by the National Bio-energy Board -- a nodal body established under the chairpersonship of the
mnes secretary. To date, about 15 such projects -- in which biogas is generated from liquid as well as solid wastes -- have been completed in various industrial sectors while 17 are underway.
One of the segments identified for the execution of this project is that of leather tanneries. In January 2000, operations commenced at a biomethanation plant at Melvisharam in
tn. Leather fleshing and primary sludge from effluent treatment plants are used at this unit. There are two similar projects in various stages of implementation in other parts of the country.
"The facility at Al-Kabeer Exports Private Limited in Medak district of Andhra Pradesh (
ap) was commissioned in November 2001 and is running very well," says Alwar Ramanujan, assistant director, department of environmental technology,
clri, Chennai. At Aligarh in Uttar Pradesh (
up), the effort is to set up a modern tannery adjacent to an abattoir. The primary advantage of such an arrangement is that waste from the abattoir can become a resource for the biomethanation plant. There is another benefit: the tannery will get fresh non-salted hides and skins, thus also greatly reducing
tds levels.
tanneries in tn: Success stories such as that of the Melvisharam plant have encouraged the government agencies to chart out a corrective course for the leather industry. Fifteen tanneries fuel the plant, with technical assistance coming from
clri. This facility generates about 1200 kilowatt hours (kwh) of power every day.
Over the years, tanneries in the state have striven hard to become environmentally compliant. But they are yet to achieve this goal fully. To be sure, the usage of chromium -- a major pollutant in tanneries -- has been drastically reduced at these sites with the setting up of several chrome recovery units. "Almost all the facilities are covered by chrome recovery units," says Sheela Rani Chunkath, chairperson, Tamil Nadu Pollution Control board (
tnpcb). This is not the case with Kanpur and Kolkata, the other major leather centres.
tn has also fared well in terms of wastewater treatment. In June 2002, there were 794 functioning tanneries in the state. About 594 out of these have been connected to 12
cetps and 200 have individual effluent treatment plants. But tanners, environmentalists, pollution control board officials and experts continue to grapple with the problem of handling
tds.
As per
tnpcb standards,
tds should be less that 2100 parts per million (ppm) in the discharged effluents. "Effluent treatment plants are able to treat the tannery wastewater and almost all the effluent parameters are met but they are not able to bring the
tds levels down to the prescribed standards," says Chunkath. The average
tds load for effluent coming out of production of a completely processed hide is about 10,000 ppm. "We are pressing them (the tanneries) to bring this down to 7500 ppm through in-plant and process modifications, which is very much possible," says S Balakrishnan, joint chief environmental engineer,
tnpcb.
ap's abattoir: Al-Kabeer Exports has a modern integrated meat-processing unit at Rudraram village, 35 kilometres from Hyderabad. It is a 100 per cent export-oriented unit with a capacity of 1500 sheep and 500-800 buffaloes per day. The waste generated during slaughtering and processing of meat is treated in biomethanation plants near the abattoir (see diagram: The mechanics of biomethanation). About 1900 cubic metres of biogas is generated from liquid wastes, thereby reducing the chemical oxygen demand content by about 80 per cent and biological oxygen demand content by 90 per cent. Solid wastes, meanwhile, help produce nearly 2250 cubic metres of biogas. The sludge from the anaerobic digester is dried and sold as nutrient-rich manure. Anaerobic bacteria break down the waste in the digester.
The technology for the facility came from Entec, Australia, and
clri, Chennai, is in charge of implementation. The single biodigester installed at the plant is designed to take 60 tonnes per day of solid wastes from the abattoir and 30 cubic metres of treated effluent sludge from the treatment plant. The hydraulic retention time (period during which the entire waste is converted into biogas) is 28 days.
The fleshings are mixed with the primary sludge and then minced. "Operating a biogas plant usually requires equal amount of water and fleshing. The primary sludge from the
cetp, which consists of as much as 80 per cent of water, is used to run the plant. This helps save large quantities of clean water," says P A Shanmugan, a senior scientist at
clri.
The mixture is then transferred into a feed chamber from where the fleshings are moved to the biodigester. The biological process that takes place inside the device involves the breaking up of organic matter by the bacteria, which leads to the release of natural gas. This consists of hydrogen sulphide, carbon dioxide and methane. The digested slurry is dried in sludge-drying beds and later sold as manure. Lime is the only chemical required during the entire process. It is needed to neutralise the acidic content of flesh.
The net power output of the biodigester and
etp is about 7680 kwh per day (kwh/d). The total electricity consumption of the entire Al-Kabeer unit is about 30,320 kwh/d. In other words, power from solid as well as liquid waste meets about 25 per cent of the total electricity demand of the Al-Kabeer factory.
"The cost of the project was Rs 3.85 crore. The total payback period is, therefore, three years which is very good," avers Ramanujan. About 4100 kg per day of residues are generated from both solid and liquid waste plants with a nitrogen-phosphorus-potassium ratio of 5: 1.1: 0.5. This manure is sold at the rate of Rs 2 per kg.
bogged down in up: The biomethanation project at a tannery in Aligarh has, however, run into rough weather. A 0.5-megawatt slaughterhouse waste-based facility was to be installed at Hind Agro Industries. There was also a plan to set up an abattoir next to a tannery. "Even civil construction work has come to a halt now," says Kanwal Jeet, technical manager, Hind Agro Industries. The imported machinery for the biomethanation plant has not yet reached Aligarh. "There seems to be some problem among the implementing agencies. We are told that it may take three to four months to resolve the issue," he adds. But Ramanujan claims that heavy rains in the region had led to the stoppage. "The project will be completed by the end of December. Imported machinery has been ordered and is expected soon," he asserts.
Reality check
Though most experts feel that Indian tanners -- especially the larger ones -- have improved their environmental performance vastly, they opine that a lot of work remains to be done. "The Indian leather industry's compliance with environmental standards is greater than that of many of its close competitors such as Indonesia, Bangladesh, China and the Philippines. But it can do better," feels Sahasranaman. "Making leather a complete bioproduct is a desirable objective. Whether it can be achieved within the tenth five-year plan period is doubtful," he says.
Environmental pressure first built up in Europe and then in the us. "But even in the developed world, processes to make leather a complete bioproduct have not emerged so far. We should, however, keep trying so that if we were to succeed, we could become the leaders," says Sahasranaman. On his part, Ramasami exudes optimism: "Give us some time and we will achieve success." Will leather weather?