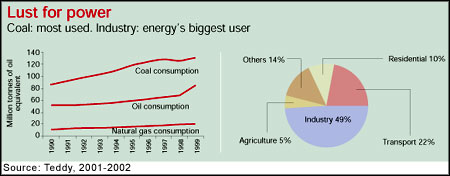
Ineptly. One word that describes the way Indian industry produces and gobbles energy. And because it is inept, it gobbles more than what is necessary. The end result: more pollution.
This, in essence, is the problem with the use of energy in India. Total energy consumption in India is climbing at a rate of 5.5 per cent per annum; and industry is the largest consumer. Between 1990-2001, for every additional Rs 1,000 in its national income, India consumed about 0.023 tonnes of oil equivalent (TOE) of energy. Compare this energy intensity to that of some developed nations: 0.002 in Switzerland, 0.0035 in the United Kingdom and 0.0052 in the US.
In terms of the environment, this high energy intensity, that has remained unchanged for the last two decades, means more pollution. Coal, which accounted for 55 per cent of India's total energy consumption of 202 million TOE in 1999-2000, disgorges 100-125 million tonnes of fly ash annually. Nearly 90 per cent of this residue is dumped as slurry in ash ponds -- an operation that uses up and pollutes huge amounts of water and creates wastelands. Emissions from petroleum-based fuels (which account for about 36 per cent of India's total primary energy consumption) as well as coal are taking a huge toll on human lives in our cities.
But India
needs all the energy that it can get. According to the
Annual Reports of the Union ministry of power (MOP), the country currently has a power deficit of 7.8 per cent -- a major hurdle for its economic growth. The challenge, therefore, lies in meeting the galloping demand for power without devastating the environment.
To square up, the country will have to get over its ineptitude. It will have to focus on cleaner generation, better consumption efficiency, multi-pronged transportation planning and a shift to a non-carbon fuel-based economy.
Clean the coal
In 1999-2000, 52 per cent of the total coal consumed in the country (76.20 million TOE) was used for power generation by thermal power plants (TPPs). The net power generated from this coal -- after accounting for conversion losses in generation (49.98 million TOE) and auxiliary generation in power plants (2.36 million TOE) -- was just 23.86 million TOE: meaning a power generation efficiency of 31.3 per cent. If we take into account transmission and distribution (T&D) losses of about 8 per cent of gross coal input, the total power generation efficiency from coal stood at a bare 23.3 per cent.
This unbelievably inefficient generation is at the core of all the energy challenges facing the nation. And it is powered by obsolete and wasteful combustion technology and poor quality of coal.
So what is the Indian government doing about it? In its Blueprint for Power Sector Development (2001), the MOP states that India will need an additional 100,000 megawatts (MW) of power by 2012. And this demand will be met not by improving technology to clean the coal and enhancing existing generation efficiency, but mainly by constructing additional power plants at an investment of Rs 800,000 crore.
The MOP's blueprint also promises the introduction in India of what it calls super critical technology, which has slightly higher efficiency than the existing TPPs. However, what it conveniently bypasses is that this version is just a modification of the existing technology, spews forth the same amounts of fly ash and is already considered obsolete in the West. With the gargantuan scale of the challenge it faces, India can do without half-baked solutions such as these. What it needs instead are clean coal combustion technologies such as fluidised bed combustion (FBC) and integrated gasification combined cycle (IGCC) that promise significantly higher efficiency and lower pollution. While FBC is a proven tech nology in India, IGCC is still in its infancy. However, IGCC offers a more efficient way of generating power: it uses high-pressure coal gases exiting a gasifier to power a gas turbine, and the exhaust from the gas turbine to run a conventional steam turbine. This 'combined cycle' turbine arrangement, not feasible in conventional combustion, gives IGCC an efficiency potential of 60 per cent compared to conventional combustion plants' 30 per cent. Investment in research and local adaptation of IGCC is, therefore, the imperative.
The FBC technology, which is currently available till IGCC becomes viable, has its advantages. Retrofitting existing TPPs with FBC can increase the energy efficiency level to 40-45 per cent. The economics of this transition also seems to be sound. According to the estimates of the Green Rating Project, India can upgrade its entire existing TPPs' capacity (about 74,700 MW) to FBC technology within the MOP's budgeted investment of Rs 800,000 crore, and still have Rs 575,900 crore left over for capacity addition and augmentation of T&D infrastructure .
The country's TPPs generation capacity, thus, can get a 45 per cent jump with an investment which is only 30 per cent of the projected Rs 800,000 crore (see box: A case for clean coal combustion technology) -- without any additional consumption of coal or construction of new power plants.
The MOP's policy on the size of its proposed plants is also a bloomer. It envisages setting up large TPPs (more than 600 MW capacity), which entail centralised generation and distribution spread across a vast area. Though large TPPs can lay claim to improved efficiency of scale, the poor status of T&D infrastructure and management in India will eliminate this advantage. Moreover, such a policy will put breakers in the way of a shift to decentralised, renewable energy technologies that seems to be the future.
Reexamine the rules
Industry, the largest consumer of energy in the country, accounts for about 49 per cent of the total commercial use; coal and lignite meet about three-fourth of this demand. As with generation, inefficiency marks the consumption of energy in India.
Within industry, the iron and steel sector leads in consumption with around 10 per cent of the total. Energy costs represent about 30-35 per cent of the total production cost in the sector. Despite this, the average energy consumed for making one tonne of crude steel in India is in the range of 30-40 GJ -- very high compared to global standards (18-20 GJ) (see table below: Abuse of power).
Abuse of power
India: low on energy efficiency |
Industry |
Average energy
consumption in India |
Global
standards |
Iron and steel |
30-40 GJ/mt crude
steel1 |
18-20 GJ/mt crude
steel2 |
Aluminum |
90 GJ/mt
aluminum3 |
60-70 GJ/mt
aluminum4 |
Mineral oil and
petroleum |
7-10% of the total oil
produced in refining5 |
5-6% of the total oil
produced in refining5 |
Paper |
35-50 GJ/mt
paper6 |
20-25 GJ/mt
paper6 |
Sources: 1. Energy Consumption in Crude Steel Production in India, Teddy, 2001-02; 2. Integrated Pollution Prevention and Control (IPPC): Reference Document on Best Available Techniques on the Production of Iron and Steel, European Commission, 2001; 3. Energy Consumption in Indian Aluminum Industry, Teddy, 2001-02; 4. Integrated Pollution Prevention and Control (IPPC): Reference Document on Best Available Techniques in the Non-Ferrous Metal Industries, European Commission, 2001; 5. IOC: Application for Best Environment Managers Award, CSE, New Delhi, 2002; 6. Green Rating of Indian Pulp and Paper Sector, CSE, New Delhi, 1999 |
|
India currently produces 20 million tonnes of steel. Assuming that the average energy consumption for making one tonne of crude steel is reduced from the current 35 GJ/tonne to 25 GJ/tonne through technology upgradation and conservation measures, the energy saved from this sector will be a whopping 200 million GJ (55,000 million KWH electricity) annually. In 2000-01, the power deficit in the country stood at 39,812 million KWH. Which means, enhancing the energy efficiency of the integrated iron and steel sector alone can meet the current power deficit in the country.
Similarly, the aluminium sector, the second largest energy consumer in India, can meet around seven per cent of India's current power deficit. The energy consumed in producing one tonne of aluminium in India is 90 GJ, compared to 70 GJ in Europe. India's average annual aluminium production is about 0.5 million tonnes. Bringing the Indian aluminium industry to European consumption levels can save about 2,750 million KWH of energy.
Efficiency of use is, evidently, the key for Indian industry, which has an immense potential for generating surplus energy. But official myopia -- exercised through illogical regulations -- has been its bane. For instance, factories in India have to pay a tax to state electricity boards (SEBs) to set up their captive power plants. And even when they generate surplus power, industries find it difficult to sell it. Selling power to SEBs is not an option because of their dismal payment record. Except for aluminium, no major energy-consuming sector sells electricity to the grid willingly. This is exemplified by the fact that of the total captive power generated within Indian industry in 2000, only about 6.4 per cent was added to the grid. Along with encouraging better energy management and technologies, the government will have to reexamine its policies for effectively meeting India's challenges of energy consumption. Renew the potential
With depleting global carbon-based fuel reserves and ever-burgeoning oil bills, India needs to reach for viable options, such as technologies that use renewable natural resources like biomass, water, wind and solar energy. The development and promotion of these technologies -- an immense potental for which exists in the country -- was started more than a decade ago. But even today, their contribution has reached just 3,000 MW-- less than 3 per cent of the total grid capacity. (see table below: Untapped)
Untapped
India's renewable energy potential |
Source/system |
Approximate
potential
|
Achievements** |
Solar photovoltaic power |
-- |
1.90 MW |
Wind power |
45,000 MW |
1,617 MW |
Small hydro power (up to 25 MW) |
15,000 MW |
1,437.47 MW |
Biomass cogeneration power
Biomass gasifier |
19,500 MW*
-- |
381.3 MW
51.3 MW |
Energy recovery from wastes |
1,700 MW |
21.98 MW |
Note: * Including biomass gasifier **
(up to 31.03.2002)
Source: Annual Report 2000-01, MNES |
|
For renewable technologies to penetrate energy use, governments and industry will have to do more than utter pretty words. In many countries, energy regulators have mandated the use of renewables by requiring industries to source a certain proportion of their energy requirements from renewable technologies. Inevitably, India and its industry need to look beyond solar cookers and streetlights. They need to think beyond oil and carbon fuels. They need to rationalise generation and consumption processes and review priorities and policies. Because in the way towards establishing a fine balance between progress and environment, this is what makes sound geopolitical and economic sense.