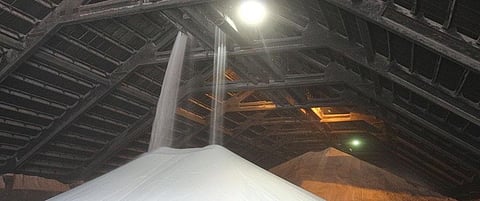
After rating six major industrial sectors in the past two decades, Delhi-based non-profit Centre for Science and Environment’s innovative Green Rating Project (GRP) assessed the fertiliser manufacturing sector in 2018-19. Before this, pulp and paper, automobiles, chlor alkali, cement, iron and steel and thermal power went through India’s only independent and rigorous environmental rating project.
The rating encourages companies to voluntarily participate. But if they do not, they are still rated based on secondary information. The principle behind this evaluation is that though profit is a private concern of industry, pollution is a public one.
The fertiliser industry touches the lives of millions of farmers. Chemical fertilisers played a key role in increasing India’s food production from 52 million tonnes (MT) in 1951 to over 277 MT in 2017-18. The annual consumption of fertilisers, in nutrient terms—nitrogen (N), phosphorus (P) and potassium (K)—has also increased from 0.07 MT to 40 MT and per hectare (ha) use from under 1 kg in 1951-52 to 135 kg in 2017-18.
Urea manufacturing is the mainstay of the fertiliser industry. Of the over 41 MT fertilisers produced in 2016-17, urea constituted around 60 per cent. India’s urea consumption has grown from 6 MT in 1980 to 30 MT in 2017.
Indigenous urea production has played an important role in fulfilling the urea demand, with the average annual production at around 24 MT in 2017—the rest is imported. Since urea production is mostly indigenous and large-scale, it was considered for GRP.
ALL OF INDIA’S 23 operational urea plants were surveyed for the project. GRP rated them on six categories comprising 54 indicators covering their entire life cycle—from environmental impact of raw material sourcing to the final product.
Under GRP, companies are sent a questionnaire and the responses are quantitatively and qualitatively assessed. Due cognisance is also given to the perceptions of local community, media, state pollution control boards and the GRP team’s first-hand observations.
Urea manufacturing is an energy intensive process, accounting for 70-80 per cent of production cost. Hence, energy use and greenhouse gas (GHG) emissions were given the highest weightage (30 per cent). Pollution—of air and water, and generation of solid and hazardous waste—is the second-most important segment and carries nearly 20 per cent weightage. Water use efficiency was given 15 per cent weightage.
Environment management systems, health and safety and compliance are crucial components of a sustainable industrial operation and 17 per cent weightage was assigned to them. Local stakeholders play the role of a watchdog in a plant’s performance and their perspective is given a weightage of 10 per cent. Transparency has been given a weightage of 8 per cent considering public disclosure practices of environmental data by the plants and their disclosure during the GRP process.
Since 1997, the Centre for Science and Environment has been rating industrial sectors through its “Green Leaves Award”. “5 Leaves” are for best performers. The urea sector as a whole received a score of 42 per cent and “3 Leaves”—an average performance.
It was, however, found to be relatively non-transparent. Of the 23 plants rated, only one managed to bag “4 Leaves” Award with a score of 61 per cent (see ‘Who stands where’ on p58). About two-thirds of the plants received “3 Leaves”. Four plants received just “1 Leaf”.
The sector has done reasonably well in implementing policy and environment management systems. The fertiliser sector is a significant contributor to India’s GHG emissions. Natural gas is the major raw material for ammonia manufacturing and hence for urea.
The urea industry, with 30 per cent, is the biggest consumer of natural gas in India. Natural gas is commonly used as feedstock and fuel, a cleaner fuel compared to naphtha—the sector though still has three naphtha-based plants. Moreover, captive power generation at all the top performing plants is gas-based—a lesson for those urea plants that run on coal-based power.
The sector as a whole received a score of 43 per cent in energy use (see ‘Energy performance’) and GHG emissions. On an average, the plants surveyed consume 6.2 Gigacalorie (GCal)/tonne of urea produced, which is nearly 30 per cent higher that the global best practice of 4.8 GCal/tonne. But some plants, like Yara, Babrala, are among the world’s best.
Emissions from production are only a small part of the GHG released from fertilisers. The bulk of CO2 emissions come from the use of fertilisers in the field, which also gives rise to emissions of the potent GHG nitrous oxide (N2O). GRP, however, did not rate the plants on emissions during the use as reliable information was not available.
FERTILISER PRODUCTION IS a moderately water intensive process. The average annual water consumption of the urea manufacturing sector of India is about 191 million cubic metres. The sector obtained an average score of 40 per cent in water use efficiency.
Plants were rated on indicators like water sourcing, specific water consumption (SWC), trends in SWC, groundwater stress, water accounting and reporting, cooling tower technology and rainwater harvesting. Indo Gulf Fertilisers (IGF) in Uttar Pradesh topped the list with a score of 66 per cent and NFL Nangal was at the bottom with a score of 15 per cent.
The average specific water use was in the range of 4.55 cubic metres/tonne to 12.73 cubic metres/tonne of urea produced (see ‘Water consumption’). Based on sector-wise comparison, public sector plants have the highest average SWC of 8.13 cubic metres/tonne urea produced in which plants with coal-based captive power plants (CPPs) are the most inefficient.
Some plants do not even meet the 2003 Corporate Responsibility for Environment Protection Guidelines, issued by the Central Pollution Control Board (CPCB).
Use of groundwater is surprisingly high with about 26 per cent plants relying on it. Four plants, all in Uttar Pradesh, rely entirely on groundwater. Together, these plants account for 94 per cent of the groundwater consumption by the urea manufacturing sector.
INDIA’S FERTILISER INDUSTRY is classified under the “red category” of polluting sectors by CPCB. Wastewater generated at urea plants contains ammoniacal and Kjeldahl nitrogen, and cyanides in varying concentrations, which can lead to groundwater and surface water pollution, if not treated properly.
At a urea plant, the major sources of water pollution are the process condensate generated from the urea section (containing urea, ammonia and CO2) and oil-bearing effluent from pumps and compressors. A substantial quantity of wastewater is also generated from plant utilities as cooling tower blow-down, demineralised regeneration and water treatment plant (WTP) back-washing. Typical end-of-pipe effluent treatment plants are generally not seen in urea plants as they possess in-house treatment facilities.
About 57 per cent samples collected near 14 plants were found non-compliant with fertiliser effluent discharge norms set by the Ministry of Environment, Forest and Climate Change, particularly with respect to cyanide concentrations in many of the samples and total Kjeldahl nitrogen levels in a few samples.
About 83 per cent groundwater samples collected near 18 plant sites had an ammoniacal nitrogen content of 0.51–93.5 parts per million (ppm), the upper limit of which is 187 times the permissible limit of 0.5 ppm for drinking water set by the Bureau of Indian Standards. Since discharges from urea plants are used in horticulture and green belt development as well as for deashing purposes, they are likely to percolate into the groundwater table.
Air pollution is more of an issue for only naphtha-based plants or those with fuel oil or coal-based captive power plants. NOx emission norms for reformers were only introduced in December 2017.
As per CPCB guidelines, it is mandatory to install continuous emission monitors (CEMS) in urea prilling towers (where urea prills or pellets are formed) but due to lack of suitable technology most urea plants with natural draft prilling towers have not been able to install CEMS. The industry emits air pollutants such as particulate matter and oxides of nitrogen, sulphur and carbon dioxide.
In general, plants are disposing their solid and hazardous wastes in the prescribed manner and are transparent about the recyclers to whom they sell their waste. Improper maintenance of ash ponds has emerged as an issue with coal-based CPPs. At some plants, fly ash ponds are not properly lined and there are no dust suppression measures in place.
THE SECTOR PERFORMED poorly in stakeholder perspective with the average score being just 32 per cent. This is largely due to poor Corporate Social Responsibility (CSR) performance of most plants. Ammonia smell is the most prevalent issue but very few plants are running community awareness and training programmes on emergency situations arising due to gaseous leakage.
Several complaints from local communities on deterioration of groundwater and surface water near plants have been received over the years due to effluent discharge. Since groundwater and effluent samples collected by the GRP team were found to be non-compliant, these complaints seem to be justified.
IFFCO, the largest cooperative and NFL, the largest public sector entity, operating three and four plants respectively (constituting around 18 per cent and 16 per cent of the total capacity of the sector respectively), proved to be big disappointments. Repeated attempts to convince them to join the responsible participating companies failed to elicit a response. These plants were rated based on the secondary information collected and local stakeholder surveys carried out.
In terms of energy consumption and CO2 emissions, NFL plants located in Bathinda, Nangal and Panipat were amongst the poor performers. In the overall water use efficiency rating, NFL, Bathinda and Panipat plants obtained only “1 Leaf”, while NFL Nangal did not even manage one.
These plants are performing even worse than high energy consuming naphtha-based plants. Also, these plants (including NFL Vijaipur I) were amongst the 14 plants that failed to meet the New Urea Policy 2018 targets set by the government and were granted additional two years to meet their targets by 2020. In terms of water efficiency also, all coal-based NFL plants are lagging, with NFL Panipat plant consuming as high as 12.7 cubic metres/tonne of urea produced.
Madras Fertilisers Ltd (MFL), a Public Sector Undertaking in Chennai performed poorly in almost all the categories and managed to get only 22 per cent.
Its average specific energy consumption during the past three years was at 7.64 GCal per tonne urea produced—the lowest in the sector. CPCB had issued directions to MFL for failing to install CEMS and continuous effluent quality monitors (CEQMS) and, thereafter, closure notice was issued to the plant in 2017. Media has reported MFL’s pollution issues regularly. As per community complaints, the plant continues to pollute the surroundings.
THE THREE TOP rated urea fertiliser plants are IGF, Jagdishpur, Uttar Pradesh at the top position; KRIBHCO Ltd, Hazira and Mangalore Chemicals and Fertilisers, Karnataka at joint second; and Yara Fertilisers, Uttar Pradesh, at the third position.
IGF is a natural gas-based plant of the Aditya Birla Group. It has an annual production capacity of 1.1 MT. The plant’s average energy consumption in the last three years has been 5.27 GCal per tonne urea produced, around 10 per cent higher than the global best practice.
Average CO2 emission intensity in the same period has been 0.44 tonne CO2 per tonne urea produced—among the best in India. The average SWC as reported by the plant is 5.09 cubic metres/tonne urea. Water accounting and metering system is in good shape and water meters are present at all important use locations. The plant was extremely transparent throughout the rating process.
KRIBHCO, Hazira is a natural gas-based plant. It has an annual urea production capacity of 2.2 MT. The plant’s average energy consumption during the last three years has been 5.66 GCal per tonne urea produced. Average CO2 emission intensity in the last three years has been 0.5 tonne CO2 per tonne urea produced—comparable to other energy-efficient plants.
In terms of water efficiency, the plant has the lowest reported SWC of 4.55 cubic metres/tonne urea—the best in the sector. The plant has been running trials to supply its wastewater to nearby industries for reuse. The treated water from its STP is utilised for cooling tower make-up. The plant has installed low-NOx burners and CEMS at its CPP gas turbine. Effluent samples collected from the plant were well within the norms for ammoniacal and Kjeldahl nitrogen.
Local community had mixed opinions about the plant. Although the plant provides drinking water to a few nearby villages, it has not undertaken any CSR initiatives in the area. The plant scored well in transparency for sharing data voluntarily and for responding to queries.
Mangalore Chemicals and Fertilisers Ltd in Panambur, north of Mangaluru city has an annual production capacity of 0.42 MT. The plant’s average energy consumption during the past three years has been 6.46 GCal per tonne urea produced. Its specific energy consumption is expected to fall once a natural gas-based supply system is established. In terms of energy consumption, the plant is performing better than the other two naphtha-based plants in India and also better than a few natural gas-based plants.
Average CO2 emission intensity during the past three years has been 1.13 tonne CO2 per tonne urea produced, which is on the higher side due to naphtha and furnace oil consumption. Its average SWC during the last three years has been 5.34 cubic metres/tonne urea produced. The plant has a zero liquid discharge system at the effluent treatment plant which allows it to completely recycle the effluent within its premises.
Yara Fertilisers acquired Tata Chemical’s Babrala unit in January 2018. It is a natural gas-based plant and the total revamped capacity of the unit is 1.28 MT. The plant’s average energy consumption during 2015-17 was 5.17 GCal/tonne urea produced—the best among all plants. Average CO2 emission intensity during the past three years has been 0.43 tonnes CO2 per tonne urea, which is among the best in India. The main source of raw water for Yara Fertilisers is groundwater obtained through borewells.
Average SWC of the plant was 4.61 cubic metres/tonne urea produced during 2015–17. Water scarcity is an issue in the region, so the plant should curtail the use of ground-water and switch to other sources. As per the plant’s compliance report, about 80 per cent treated waste-water is recycled in process and the rest is used in landscaping. The plant’s CSR activities were appreciated by nearby villages during the survey. However, the plant performed poorly in terms of transparency by not sharing any information.
THE FERTILISER SECTOR is the most controlled sector of the Indian economy. Over the last 60 years, the control of the government over urea has only tightened. Not even a kilogram can be produced or sold without the government’s authorisation. Urea subsidy is one of the most micro-managed one. Due to the widening gap between cost of production and retail prices and the manifold increase in consumption, the fertiliser subsidy has increased drastically.
Among large developing economies, Indian farmers pay the lowest price for urea. This under-pricing has serious consequences. The use of urea often comes at the cost of other fertilisers and nutrients that are essential for the growth of plants. As fertilisers other than urea are partially decontrolled, their prices have increased relatively. The result has been a disproportionately higher use of urea.
While the desirable ratio of N-P-K application is 4:2:1, the ratio in Punjab stands at 31.4:8:1 and the ratios are also skewed in favour of nitrogen in most other regions. This imbalance in plant nutrition has caused many problems, such as stagnating or even declining productivity, soil sickness, widespread deficiency of secondary and micronutrients, and soil alkalinity and salinity.
As urea subsidy is universal, rich farmers tend to benefit more from it. Local retailers artificially reduce availability in order to redirect farmers to the black market. Entrepreneurial large farmers and local shops buy large quantities, to be resold for profit. The more serious leakages occur from agriculture to industry and across international borders. Putting all leakages and inefficiencies together, it is estimated that only 34 per cent fertiliser subsidy manages to trickle down to small and marginal farmers.
The overall financial health of the urea industry is poor. Even the profitability of the best performing companies in the fertiliser sector is far lower than their peers in other core sectors of the economy.
The biggest issue facing the sector has to do with the future of nitrogenous fertilisers. The industry has an important role to play in addressing two major global environmental challenges: nitrogen pollution and climate change. Moreover, the world has breached the planetary limit for nitrogen, and the use of nitrogenous fertilisers is a major contributor. Nitrogen pollution of surface and groundwater has reached alarming levels in many states of India.
TODAY, THE FERTILISER industry stands at a crossroads. It is a relatively energy-efficient sector of the economy but it has disregarded environmental issues, in particular its water footprint and pollution. Improving the environmental performance of the urea sector requires multi-directional initiatives.
Plants can reduce their water footprint by investing in rainwater harvesting within and outside the premises to recharge groundwater. They should strive to become water-neutral by recharging more ground-water than they withdraw.
Plants must try to achieve zero liquid discharge status by adopting advanced tertiary treatment technologies, and use treated water for cooling tower and boiler make-up. They should also replace the practice of wet ash handling and shift to dry ash handling for water conservation and to maximise utilisation of fly ash.
The use of coal for captive power needs to be phased out. NOx and ammonia emissions need to be controlled. Particulate emissions from prill towers also need to be curtailed. The sector also needs to install CEMS for online monitoring of pollution levels.
The emission and effluent discharge standards were amended almost after three decades in December 2017, but even these revised standards are quite lax in comparison to global norms, and need to be tightened.
The sector needs to invest in technologies for pollution control, such as NOx control in stack, dust emissions abatement at prilling towers, ammonia emissions curtailment, and advanced water treatment. It is vital that the government provides reimbursement for such investments. This will not only improve resource efficiency of plants but will also reduce local environmental impacts due to plant operations.
Indian agriculture needs to graduate from the present practice of bulk application of fertilisers to a more precise supply of required nutrients. Nitrogen use efficiency in India is very low, at below 35 per cent in lowland rice and under 50 per cent in upland crops. The rest of the nitrogen is lost to the environment, representing a significant financial loss as well as contributing to pollution.
The sector must go from being a volume driven industry which measures its performance by tonnes of urea produced, to a functionality driven industry which measures its performance by improved soil health and better yields.
Bio-fertilisers are one product that can be profitable to industry and farmers as well as being less harmful to the environment. While the fertiliser industry already produces and sells bio-fertilisers, it needs to do more in this potential growth area.
As organic fertilisers and compost come with a much lower environmental footprint than synthetic fertilisers, the industry should do well to take up the organised production and distribution of the same.
In a climate constrained world, the production of nitrogenous fertilisers will have to shift from fossil fuels to renewables. The falling costs of renewable energy will make this fiscally feasible. Yara is already setting up a small solar-powered electrolytic plant to produce hydrogen for ammonia production at its facility in Pilbara, Australia.
Fertilisers are the most controlled sector of the Indian economy. The system of subsidies and controls in its present form has led to imbalanced and gross overuse of urea with adverse consequences both for the environment and for agricultural productivity. Further, it neither benefits the small farmer nor does it support the industry adequately.
Industry has to struggle with a Kafkaesque bureaucracy micro managing marketing, logistics and subsidy payment, which has seriously vitiated the business environment in the sector. Thus, for the fertiliser industry to take the required steps the government needs to bring a measure of decontrol in the industry. Decontrol will also make the industry more competitive.
Competitiveness and innovation will be vital for the survival and growth of the industry in the 21st century.
(The article is based on a CSE report titled Grain by Grain: Green Rating of the Fertilizer Sector, released on June 5, 2019)
(This article was first published in Down To Earth's print edition dated June 1-15, 2019)