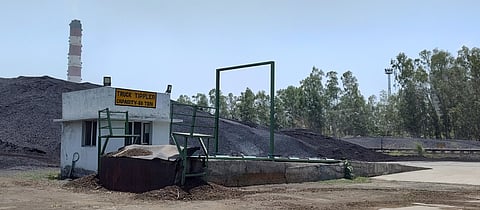
Unavailability of biomass pellets of agricultural residues is emerging as a dampener in implementing the Union power ministry’s direction to co-fire biomass with coal in thermal power plants.
Substituting 5-7 per cent of coal with biomass in coal-based power plants can save 38 million tonnes of carbon dioxide emissions, said finance minister Nirmala Sitharaman in her budget speech in 2022. However, the existing infrastructure may not be robust enough to turn this into reality.
Around 95,000-96,000 tonnes of biomass pellets are required per day for co-firing, according to the ‘National Mission on use of biomass for coal thermal power plants’ set up by the Union power ministry. But India’s pellet manufacturing capacity is 7,000 tonnes per day at present despite a surplus 228 million tonnes of agricultural residue available in the country, the department data showed.
The department informed that the manufacturing capacity may be expanded soon.
This demand-supply gap has further intensified in the last two months. This is because pellet suppliers favour selling their product to industries such as textile, food processing, metal based or in open market at Rs 12-13 per kilogram (even higher in some places in Punjab), instead of supplying it to coal thermal power plants at the offered price of Rs 8-9 per kg.
Earlier last year, the NTPC-Dadri was procuring biomass pellets at only Rs 5.35 per kg.
Biomass demand of industries escalated since the Commission for Air Quality Management in National Capital Region and Adjoining Areas directed industries in Delhi-National Capital Region to switch to cleaner fuels by end of September 2022.
To date, 36 gigawatts of coal-based thermal power capacity in the country has successfully co-fired biomass. But several of these plants have only carried out trial-runs and are in the process of required modifications and upgrades in the plant to accommodate biomass co-firing at 5-10 per cent.
Coal power plants that successfully co-fired biomass
Developer |
Capacity (MW) |
NTPC |
25,830 |
Haryana Power Generation Corporation Ltd (HPGCL) |
1,800 |
Larsen & Turbo (L&T) |
1,400 |
Adani Power |
1,320 |
Apraava Energy (China Light Power) |
1,320 |
Jaypee Group |
1,320 |
Jindal Power Ltd |
1,000 |
Calcutta Electric Supply Corporation (CESC) |
750 |
Dhariwal Infrastructure Ltd (wholly owned subsidy of CESC) |
600 |
Haldia Energy Ltd |
600 |
Uttar Pradesh Rajya Vidyut Utpadan Nigam |
500 |
Source: Union Ministry of Power (May 2022)
Several coal-based power generators such as HPGCL, Jindal India Thermal Power Ltd, Nabha Power Ltd, Hiranmaye Energy, Gujarat State electricity Corporation Ltd (GSECL) have issued tenders for supply of biomass offering, a seven-year contract to successful bidders to ensure a long-term continuous supply of biomass.
Skewed demand-supply
NTPC-Dadri started co-firing biomass in November 2019 after demonstrating successful trial runs in 2017. But the co-firing is being done only intermittently based on the availability of biomass.
The plant uses around 25,000 tonnes of coal for daily generation. In the last two-and-a-half years, however, it has co-fired only 20,000 tonnes of biomass, officials informed the Centre for Science and Environment, a Delhi-based non-profit.
This huge gap is due to the seasonal availability and unreliable supply of biomass pellets to the utility.
The Mahatma Gandhi thermal power plant by the CLP group in Jhajjar has also co-fired biomass only 70-75 times till date from the first trial-run in February, 2022. At present, their boiler can only co-fire at 0.2-0.5 per cent as opposed to the mandatory minimum of 5 per cent.
To enhance co-firing, process changes such as creation of separate bunkers for feeding biomass into the mill for crushing will need to be made. The process changes are still under review.
The plant has a bowl mill and can only use biomass that is torrefied (preheated at 250-300 degrees Celsius to remove volatile matter and reduce moisture). There are even fewer suppliers of torrefied pellets in the market.
Nabha Thermal Power Plant (L&T, Punjab), similarly, has had no takers so far for its tender on the supply of pellets. The plant has co-fired 13 tonnes of biomass only.
Nearly 0.25-0.3 million tonnes of biomass pellets are required to generate 1 GW of electricity at 7 per cent co-firing, according to the power ministry’s policy on biomass utilisation.
The ‘National Mission on use of Biomass in coal-based thermal power plants’, also called SAMARTH — Sustainable Agrarian Mission on use of Agro-residue in Thermal Power Plants — has shared a list of 70-80 pellet manufacturers with the power plants.
The government has stressed on increasing the capacity of pellet manufacturers and in this regard, several trainings for pellet manufacturers have been conducted by the National Power Training Institute all over the country.
In order to further strengthen and regulate the supply chain, the manufacturers were also asked to be registered under SAMARTH.
Down To Earth had reported earlier that the biomass co-firing can help cut emissions from the thermal power sector by 90-180 million tonnes by 2030, replacing 50-100 million tonnes of coal.
A CSE survey of the power plants in Delhi-NCR revealed that there are apprehensions among power plant operators about the continuous and reliable supply of biomass.
It is challenging to store biomass pellets for long durations at the plant sites since they absorb moisture from air quickly, rendering them useless for co-firing. Typically, only pellets with up to 14 per cent of moisture can be used for combustion along with coal.
Biomass co-firing is an effective way to curb emissions from open burning of crop residue; it also decarbonises the process of electricity generation using coal.
Mapping of existing manufacturers and incentivising entrepreneurs to set up more pellet manufacturing plants need to be explored by SAMARTH.
The mission also needs to ensure the price of biomass pellets are capped and protected from fluctuations in market demand.
Finally, and perhaps most importantly, platforms need to be established to ensure farmers have an intrinsic role in this business model of pellet manufacturing and co-firing in power plants.