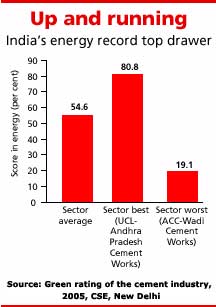
Making cement is energy-intensive. Energy accounts for a significant portion of the cost of producing cement. Most technological advancement, unsurprisingly, has been directed towards reducing its consumption. Unlike other industries in India, in which technological levels lag behind the best in the world, the cement industry is state of the art. This is the key to the Indian cement sector's competitiveness. It also makes this sector one of the most energy-efficient
(see graph: Energy drive). About 80 per cent of energy consumed by a cement plant happens in the clinkerisation process. The sector is quite efficient in utilising energy in the kiln. It is amongst the lowest compared to other cement manufacturers
(see table: Global edge). Japan scores due to its advanced technology while countries like China and the
us are the laggards, using obsolete technology.
Despite its decent performance, The cement industry can improve energy consumption by 25 per cent more than the best achievable figure of 2.65 gigajoule/tonne of clinker.
Not only is the industry thermal energy efficient, it has also managed to lower power consumption. Power in the cement plant is required for all the grinding sections -- the cement mill is most power-intensive. The Indian cement sector gains because of increased usage of flyash, which leads to a reduction in power consumption. Use of flyash reduces clinker, which requires grinding in the cement mill.
The Indian cement industry consumed on an average around 92 kilowatt-hour of power per tonne of cement, which is better than most international players. This efficiency has reduced carbon dioxide (
co2) emissions, helped by using blending material instead of clinker. In clinker formation, calcium carbonates splits to form calcium oxide and
co2. The cement industry is globally one of the major contributors of
co2, accounting for five per cent of the total
co2 emitted (
The Cement Sustainability Initiative Progress Report, World Business Council for Sustainable Development, June 2005).
The industry generates 724 kg of
co2 for every tonne of cement manufactured annually. This is low in international comparison
(see graph: Carbon care). The industry realises brownie points can be earned though the clean development mechanism which, mandated by the Kyoto Protocol, allows industries that save on green house gases to get environmental credits -- read international funding from polluters. Most big cement makers -- Gujarat Ambuja,
acc, Jaypee, Birla Corporation, Shree and Binani -- have applied for project approvals under this mechanism, on the basis of blended cement making.
In energy and technology, the sector has even performed better than other countries. The average sector score is much higher on these two indicators -- energy (54.6 per cent) and technology (48.7 per cent). The main driver is the high energy cost, which accounts for 25 per cent of turnover.