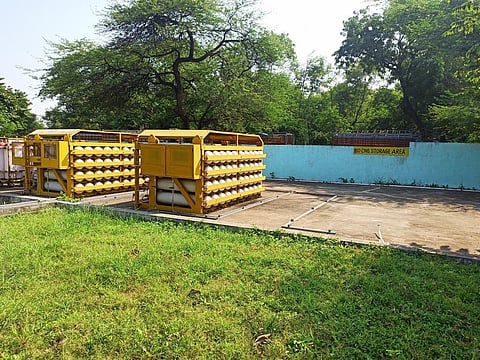
Bio-CNG, also known as Compressed Biogas (CBG), came on the Government agenda only in 2018 when the Ministry of Petroleum and Natural Gas (MoPNG) launched Sustainable Alternative towards affordable transportation (SATAT).
Before this, some plants had already started experimenting with making electricity from biogas and Compressed Biogas.
SATAT saw obvious advantages — lesser dependence on crude oil import, decarbonisation of the economy, waste management and job creation — which is a casualty in any other renewable energy source.
It was estimated that 62 million tonnes of CBG can be produced in India every year from various sources. To tap this, MoPNG announced that 5,000 CBG plants will be set up by 2025 that will produce 15 million tonnes of CBG.
At the 2018 consumption level, this was projected to take care of 40 per cent of the annual CNG requirement in the country (44 million tonnes then) and produce 50 million tonnes of bio-manure for crops.
Under SATAT, oil and gas marketing companies are supposed to pick up ready gas from CBG companies. Companies like Indian Oil, BPCL and Avantika in Indore issue letters of intent (LOIs) to CBG companies that help them apply for loans and central financial assistance for setting up the plant.
The SATAT homepage shows about 3500 LOIs issued till date all over India. However, only 37 plants have been commissioned.
“We use less than 2.5 per cent of Bio-CNG potential from MSW and wastewater. If we account for other sources such as agricultural and livestock dung, the net utilisation will be even less than 0.5 per cent of the total potential,” said Prakash Singh of IIT Guwahati.
Avantika in Indore issued 11 LOIs to interested companies.
“But only one is supplying gas. The companies are finding it difficult to generate adequate and consistent feedstock. “Unless there is a feedstock of 100 tonnes per day, it is difficult to sustain a CBG plant,” he observed.
Avantika is trying to issue more LOIs because of the rise in global prices of CNG. “We need more indigenous sources of CBG soon,” said Himanshu Srivastava, Manager, Avantika.
High capital investment is also stopping small investors from entering the CBG scene.
“If the cost of setting up compost plant for 100 TPD waste is 20-30 crores, a CBG plant for same input requires Rs 40 crores. Some 40 per cent of the investment is for setting up biogas purification infrastructure,” said SWM expert Subhashish Parida.
SATAT provides central finance assistance at the rate of Rs four crores for setting up a 4800 kg/day output CBG plant with a maximum cap of Rs 10 crore, but even that was discontinued in between.
“The subsidy they are giving is based on the market rates of machinery in 2005-2006 when I was a part of MNRE. But the cost of machinery and the daily operation cost is much higher now,” said Atma Ram Shukla of Indian Biogas Association.
Big companies like Ever Enviro can manage but small players will not be able to enter the market without Government support, Shukla added.
The feedstock for MSW-based CBG plants is source-segregated waste — also its biggest challenge.
“Badly segregated waste can lead to construction and demolition waste or other hard particles entering the digester which can not only reduce it’s energy efficiency but also damage it,” said Nagendra Kumar, CBG expert and fellow at The Energy and Resources Institute (TERI), New Delhi.
Vizag Bioenergy Fuel Pvt Ltd, a two-TPD CBG plant in Visakhapatnam, has a contract with Visakhapatnam Municipal Corporation to provide them 20 TPD of segregated biodegradable waste.
“But I still get 15-20 per cent mixed waste daily,” said KS Raja, CEO of Vizag Bioenergy.
There is no technical solution for this and we have to employ manpower which is not readily available for the same, he added.
“Since three years that I have been in this sector, I see that municipal corporations do not have the will to implement segregation. I feel they should hand over the collection job to us. Since fresh biodegradable waste is our main resource, we will be able to handle it more professionally,” he said.
Only 10-15 per cent of the entire municipal body’s budget is allocated for solid waste management, out of which 70 per cent is spent on salaries. Indore, on the other hand, is not just managing waste, but also earning revenue from user fees, carbon credits and also fines for non-segregated waste, said Swati Singh Sambyal, an independent circular economy expert.
In 2020, IMC earned Rs 9,239 lakh in revenue from user charges, while the expenditure was 8,190.66 lakhs.
For Indore, the CBG plant came five years after putting its waste segregation infrastructure in place.
Apart from collecting segregated waste at source in compartmentalised vehicles, Indore has transfer stations where waste collected in six separate categories is further sorted and transported in separate colour-coded capsules to the processing facilities for wet and dry waste.
“The transfer stations are our backbone. If not for them, we will not get this high-quality segregated waste,” says Nitesh Tripathi, plant head of Gobar Dhan CBG plant.
The entire infrastructure should support segregation rather than just penalties at household level, said Sambyal.
The coming together of political, administrative and public will is what has worked for Indore, which is missing in metros like Delhi that have set up waste-to-energy plants in the name of processing even though only 11 per cent of the city waste is worth incineration, said Sambyal.
CBG companies have to work in close coordination with urban local bodies, not just for the right feedstock on a daily basis but also for getting land and facilitating licenses and permissions.
This makes private sector investors vary, due to governance-related issues, said Nurial Pezarkar, CEO of Noble Exchange Environment Solutions, which has 14 TPD CBG plants in Pune.
The limited technical capabilities of municipal bodies act as a hindrance here. “Usually, only one person in the MSW section is in charge of multiple roles — sanitation, road sweeping, waste management — which is too much to handle,” said Sambyal.
CBG technology is in its nascent stage. There is also a lack of sector experts at the ground level. “When SATAT targets were being set, things were put in motion due to government pressure. There were many businessmen to set up plants but not enough skilled manpower to run them,” says TERI’s Kumar.
Kumar pointed out that low resource mapping of garbage in cities leads to problems later. Our lab results have shown that waste in no two cities can be the same.
In fact, it changes within the same city also from season to season. Accordingly, the CBG potential of each city is different, he said. It is a biological process — the bacteria will produce output from a given input only.
So if secondary study shows that 60-70 cubic metres of gas can be produced from one tonne of waste, the numbers in another city can vary by as much as 40-50 per cent.
Resource mapping of Indore, for instance, cannot be applied to another city. More and more testing is the only answer, Kumar explained. The Bureau of Indian Standards is working on India-specific biogas standards, according to Indian Biogas Association (IBA).
The Indore plant did face this issue when a lot of fibrous waste started coming in recently, which took more time for digestion. “We are now installing a difibrator,” said Tripathi of Ever Enviro.
The company is also setting up a plant in Bhopal that will produce 12 TPD CBG from 400 TPD waste.
“Though Bhopal has more than 90 per cent segregated waste which is ideal for us, its main challenge is garden waste. It has less methane and it also takes more time to decompose as compared to other wet waste. We are considering whether to bypass it or construct a dedicated digester tank for it where it will get more retention time,” said Azhar Sadique, plant head, Ever Enviro, Bhopal.
Under the CBG-CGD synchronisation scheme of SATAT, there is a provision for injecting CBG in the city gas distribution (CGD) network for both CNG (transport) and PNG (cooking and industry) purposes.
But the differential tax structure of CNG and CBG is a hurdle for gas distributors like Avantika from utilising this scheme.
“To encourage CBG, the government levies only 5 per cent GST on CBG while tax on CNG is 14 per cent VAT and 14 per cent excise duty,” said Manish Verma, head of marketing, Avantika Gas Limited.
Some 20-25 trucks are used to transport hazardous gas by road which also consumes a lot of fuel. We have a 5500 km long network of pipelines in Indore that can be easily connected to the CBG plant.
But the tax authorities say that once CBG is injected into the pipeline, it will be treated as CNG and would warrant 28 per cent tax which is too much for the consumer to pay, Verma added.
Unlike CBG for vehicular engines, gas used for industrial or cooking purposes does not need to be pressurised at 200-250 bars. “We need it only at four bars. Even if we are able to supply 50 per cent of our gas through pipelines, that reduces our compression cost that much,” said Tripathi.
The number of CNG stations in India is still low, which makes it difficult to sell CBG for vehicular use.
In 2021, there were only 3,180 CNG stations in India compared to more than 65,000 petrol pumps. “Lack of infrastructure could also place uncertainty in the user’s consciousness while making a purchase decision,” says the IIT Guwahati paper by Prakash Singh and Ajay Kalamdhad.
Vizag Bioenergy could not sell its gas in April this year because the dedicated CBG retail outlet in Visakhpatnam could not take the gas for some reason.
“There are two more CNG stations in the city but they refused to take the gas as they do not allow mixing due to the GST-VAT problem, even though SATAT has a provision for it,” said Raja.
SATAT has a standard rate for CBG from all sources. In Indore, it is Rs 56 per kg, up from Rs 46 per kilo till last year (or 80 per cent of the retail price of CNG). But experts feel that the production cost for each feedstock varies.
“An MSW based plant has a high pre-treatment cost because the mixed waste has to be homogenised before sending it to the digester. Agricultural residue has to be sourced from different areas while press mud or cow dung is better feedstock but sustainable only if the plant is near a sugar factory or dairy farm,” said Shukla.
With such vast differences in the processes and also availability of the feedstock, SATAT should set a differential price for each, he said.
To produce one cubic metre of biogas from cow dung requires 25 kg of feedstock, while the same quantity, if made from MSW, would require 15 kg and, if made from agricultural residue, would need five kg.
The slurry left after biogas is extracted from the digester is passed through a solid-liquid separator. The solid part is cured in the open for 10-15 days and makes for carbon-rich organic manure, while the liquid part can also be used as liquid fertiliser.
CBG companies factor in 15-20 per cent of their revenue from selling this manure.
“This manure is way better than the one produced by compost plants because it is made from pre-treated waste and in anaerobic conditions, unlike windrow composting method used by municipal bodies, which is aerobic and the compost also needs to be cleaned later,” said Tripathi.
Windrow composting releases a lot of methane into the atmosphere, defeating the purpose of waste processing as it generates another toxic gas, said Shukla.
Officially designated as fermented organic manure (FOM) in 2021, this product from CBG plants was incorporated in the Fertiliser (Inorganic, Organic or Mixed) (Control) Order, 1985.
The Ministry of Fertilisers, through an order in May 2022, made it mandatory for fertiliser companies to offtake FOM from CBG companies under SATAT as part of Integrated Nutrient Management.
But there are still no buyers. The Indore plant generated 100 TPD and the Vizag plant generated six TPD FOM.
Vizag Bioenergy is also experimenting with value-adding FOM with phosphorus. “This phosphorus-rich organic manure can replace diammonium phosphate (DAP) which the Government has to import at a massive price,” said Raja of Vizag Bioenergy.
Priced at Rs 1,500-20,00 per tonne in the open market, farmers find it expensive to buy as compared to the highly-subsidised chemical fertilisers.
“The Government should pitch in by giving subsidies on FOM if they want the entire CBG model to succeed. Farmers should also be incentivised by linking the price of organic manure to organic produce,” said Kumar.
“Since FOM is rich in carbon, it will rejuvenate the soil that has been destroyed by overdosing of chemical fertilisers which will be the actual returning back to the land, an example of circular economy,” said Shukla.
This is the last of a three-part series
This story was produced with the support of Internews’ Earth Journalism Network