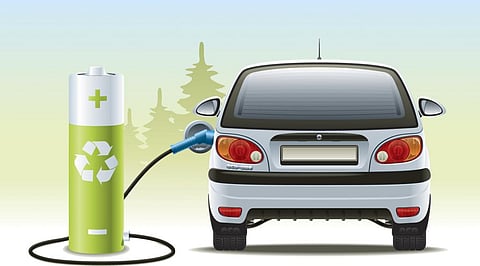
Electric vehicles will be key to decarbonising transport. The recent Battery Waste Management Rules, 2022 notified by the Narendra Modi government promises to trigger circular economy, but it needs to be designed to enable efficient and effective recycling.
One of the methods to achieve a reasonable amount of success with circularity is to follow a cradle-to-cradle trajectory for the electric cars and their batteries.
The recently released Battery Waste Management Rules 2022 by the Union Ministry of Environment Forest & Climate Change aims to achieve this by placing the producer and importer of batteries at the centre of battery recycling rules with extended producer responsibility (EPR).
The producers can meet their EPR obligation through the extended producer responsibility certificates made available by the recycler or refurbished after they recycle or refurbish the desired quantities of waste batteries.
The certificates will be generated on a centralised portal managed by Central Pollution Control Board (CPCB). The parameters for the certificates will include the weight of battery processed, percentage fulfilment of material recovery targets for the specified year and geographical source of battery.
The current version of the battery waste rules cover electric vehicle batteries, as well as portable, automotive and industrial batteries.
It builds upon and replaces the Battery (Management and Handling) Rules, 2001 to comprehensively address the changing landscape of electric vehicles and advancements in battery technologies.
Under the new rules, the producer and battery importer will be responsible for collecting and recycling or refurbishing batteries it has introduced into the market.
The best part about the new battery waste rules is that it is outcome-based and can be measurable. It defines mandatory targets for collection and recycling within a compliance timeframe.
An electric two-wheeler manufacturer has to meet a mandatory collection target of 70 per cent of batteries placed in the market in 2022-23 and has a seven-year compliance time frame starting 2026-27.
For electric three-wheeler manufacturers, the meter starts earlier in 2021-22, according to their introduction into the market and their compliance cycle starts in 2024-25. Electric four-wheelers have a longer compliance cycle at 14 years.
Producers have two ways to meet their targets. They either bear the responsibility of managing battery waste or use the EPR certificate by acquiring surplus certificates from producers of the same battery category made available by recyclers or refurbishers.
The rules provide flexibility in managing EPR certificates by making them exchangeable and tradable for fulfilling EPR targets. There are provisions for information on the amount of waste batteries as part of the EPR obligations of producers.
However, it does not provide visibility into the auditing process undertaken for producers, recyclers and refurbishers.
The framed targets are fairly granular in nature and are differentiated by the type of batteries collected (lead-acid, lithium-ion, nickel-cadmium or zinc-based batteries). Non-compliance will be penalised with an environment compensation charge. The system will also deploy a second line of deterrence in which names of defaulting entities will be made public on the CPCB website.
After processing, producers have to mandatorily use a minimum defined percentage of recycled materials recovered from old waste batteries to produce new ones.
However, the rules miss out on a huge opportunity to enable sustainability standards that have the potential to make India a benchmark for the global battery industry.
The Rules list out limits and labelling requirements for batteries. Labels have to indicate limits on the use of heavy metals — cadmium, mercury and lead — and also have a picture of a crossed-out bin to indicate that the batteries cannot be binned and have to be handed out to a registered battery collector.
With traditional batteries that were based on lead-acid and nickel cadmium chemistries, this can be a useful practice and will inform the recycling community about the need to plan for their management. It will also ensure that the producer maintains limits on the quantum of heavy metals used.
But the labelling requirements do not address issues with lithium-ion batteries. Information about lithium chemistries used in the battery on the label could enable more efficient and easier recycling processes. Different battery materials require different kinds of treatment at the recycling stage.
Lack of information about chemistries would require the recycler to deploy additional resources to investigate the materials present in the spent battery feedstock before they can be processed.
The new rules also miss out on using labels as an opportunity to reflect the battery’s carbon footprint. This would make their environmental impact more transparent, especially if it covers the entire life of the battery as well as the percentage of recycled battery materials such as cobalt, lithium and nickel.
The deployment of such a practice could have multipronged benefits.
Using carbon footprint as a parameter for producer responsibility could trigger research and development activities upstream with lower footprint materials, possibly sourced from within the country.
Lithium-ion batteries have a very high carbon footprint as they have materials sourced from various parts of the world (South America and Australia for lithium, Congo for cobalt and Indonesia for nickel).
Sourcing information can also ensure identification and avoidance of a supply chain with human rights abuse history. About 15 per cent of cobalt sourced from Congo comes from artisanal mines that often use under-aged labour.
With such tracking regulation in place, battery manufacturers will have to conduct due diligence exercises to ensure compliance.
Such regulations, however, could add to the cost of batteries. Versions of similar regulations have already initiated efforts globally for developing cobalt-free batteries with lithium iron phosphate and lithium titanate chemistries, according to the Cobalt Institute, a United Kingdom-based trade association of cobalt producers and recyclers.
Cost continues to be an issue with lithium-ion batteries. With electric vehicle battery demand at a high, the cost of raw materials has increased, leading to supply issues. Going further, many mines will have to be developed to meet new demand.
The Battery Waste Management Rules are intended to subsidise a part of that materials feed by building a stream of recycled battery materials for the new production cycle. Batteries need to be designed to enable more improved recycling. The design objective should not be just guided by extraction of resources but also lead to efficient and effective recycling process.
If larger sustainability standards were built into battery waste management, the potential for strengthening rules for design, production and disposal of batteries in India could improve. It will be more holistic in practice and govern the entire product life cycle, from the design phase to end-of-life.
If not implemented correctly, the rules could fail to promote a circular economy and even disrupt the country’s climate mitigation targets. Implemented right, it can become a platform to expand inputs to feedstock for battery manufacturing in the future. This will support future material supply security and offer cost benefits.
Recycled material is always cheaper than the fresh output from the mines. That is because the metals present in the black mass, an intermediate product derived after recycling batteries, contain battery-grade material that does not require complex extraction processes with mine output.
Cobalt is mined as a by-product in nickel and copper mines. Typically, such ores contain 2 per cent of cobalt, with 60 per cent copper and 70 per cent nickel.