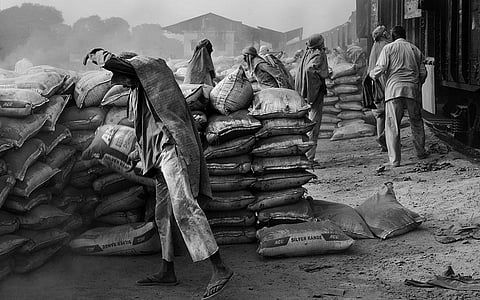
What water is to life, cement is to the modern world. Since it was developed two centuries ago during an experiment by British bricklayer Joseph Aspdin, who heated a mix of limestone and clay to form a fine powder that hardened when exposed to water, cement has become the foundation of modern civilisation. Today concrete (mainly cement) is the second most used material after water. Globally, a person uses 530 kg of cement on average in a year. The dependence on this robust and versatile construction material can be gauged from the fact that an individual in India consumes more than double the amount of cement than the staple food, rice—240 kg of cement in a year against 102 kg of rice.
The problem is that this staple of the modern life is also a major source of greenhouse gas (GHG) emissions. Production of 1 kg of cement releases almost an equal amount—up to 0.8 kg—of carbon dioxide (CO2).
According to the International Energy Agency (IEA), the sector is considered to be the second largest industrial emitter in the world, and contributes about 7 per cent of CO2 emissions globally. To put it in perspective, if the cement industry were a country it would be the third-largest emitter of CO2, after the US and China.
With growing demand for cement, which is key to economic growth and development of a nation, the industry is set to produce more and emit more. In the past three decades, the world has seen a threefold increase in cement production. Yet-Ming Chiang, Kyocera Professor of materials science and engineering at the Massachusetts Institute of Technology (MIT), US, who has been working on ways to eliminate carbon emissions from cement production, estimates that the number of buildings worldwide is expected to double by 2060. The commodity is now very cheap to produce: It costs only about 13 cents (22 paise) per kilogram, which makes it cheaper than bottled water, he was quoted as saying by MIT News in 2019. A report by Market Research Future, a Pune-based analysis firm, says the world cement market will grow at a compound annual growth rate (CAGR) of 5.3 per cent till 2030.
Decarbonising the cement sector is thus critical to slow global warming. To limit global temperature rise to 1.5oC above the pre-industrial levels and to avoid the worst climate impacts, global GHG emissions will need to reduce by nearly half by 2030 and ultimately reach “net-zero”, which the UN defines as “cutting GHG emissions to as close to zero as possible, with any remaining emissions re-absorbed from the atmosphere, by oceans and forests for instance”. A growing number of countries, cities, businesses and other institutions are making commitments to reach “net zero” emissions by 2050 (or by 2070, as pledged by India). IEA says the global cement industry, the second largest industrial emitter (after iron and steel), must cut its CO2 emission by 3 per cent every year till 2030 to get on track to meet net-zero emissions by 2050.
But this is easier said than done. Unlike most other materials, CO2 emission is intrinsic to the very chemistry of cement. In other words, CO2 is emitted not only from the burning of fuel during the manufacturing process, it also forms during the synthesis of the cement compounds.
During the production of cement, the raw materials, typically limestone and clay, are heated in a kiln at more than 1,400oC in a process called pyro-processing. Upon heating, calcium carbonate (CaCO3), the principal constituent of limestone, breaks up to release CO2. This process is known as calcination. The remaining calcium oxide (CaO), also known as quicklime, then combines with aluminium silicates present in clay to form molecular complexes such as calcium silicates. These clinkers or small lumps of stony residues are then milled and combined with ingredients like gypsum to produce cement. Scientists say more than 50 per cent of the CO2 emissions from cement-making result from calcination. The remaining is released from burning of coal and other fossil fuels during pyro-processing and other processes involved in manufacturing and from use of electricity to power the processes (see ‘Emission-intensive manufacturing’, p35). This means switching to low-carbon fuel or renewable energy alone will not help decarbonise the cement sector. Reducing the consumption of cement is also a near impossible proposition; for one, cement has few practical alternatives, and two, it is linked to the huge need for housing and infrastructure across developing countries, including India.
Decarbonising the sector poses a complex challenge for India, which is one of the fastest urbanising countries and is witnessing a housing and infrastructure boom. India at present is the second largest cement producer after China, which accounts for more than half of the global production. Think tanks like the Alliance for an Energy Efficient Economy say that CO2 emission intensity of the Indian cement industry is less than the global average. Yet, emissions from the sector saw a 246 per cent rise during the two decades between 1994 and 2016, according to India’s third “Biennial update report” (BUR), which the government submitted to the UN Framework Convention on Climate Change (UNFCCC) in 2021 to update on its GHG inventories and mitigation actions. This was proportionate to the country’s cement production, which grew five times during the period (see ‘A booming sector’, p30). In 2021, India’s cement sector contributed 5.63 per cent of its total GHG emissions in 2016, states the update report.
Over the next few years, estimates IEA, India will see its cement industry expand at a rate higher than the world average. Kanvic, a Delhi-based management consulting firm, projects that the country will produce 660 million tonnes of cement in 2030, up from 334 million tonnes in 2019-20 (see ‘Future surge’). Various estimates analysed by the Centre for Science and Environment (CSE), a Delhi-based research and advocacy organisation, also indicate that cement production in India will rise at a CAGR of 6-8 per cent till 2030. CSE researchers estimate that in a business as usual scenario, emissions from India’s cement sector will nearly double by 2030, from the 213 tonnes of CO2 released by the sector in 2019-20.
As of now, India does not have a climate change abatement roadmap for the cement sector. There are only a few schemes and economic instruments that encourage the sector to improve its energy efficiency and reduce its carbon footprint by using industrial waste such as fly ash as raw material. Then how does a carbon-intensive sector such as the cement industry maintain a high growth trajectory and at the same time reduce its GHG emissions with urgency? The answer to this question is crucial not only to India’s economic growth and development but also to its climate commitments.
Over the past one year, CSE researchers have conducted an extensive analysis of cement plants in the country to explore ways to reduce the carbon footprint of this hard-to-abate industry. Based on the plants’ production volume, fuels and raw materials used, CO2 emissions released and ambition to reduce carbon footprint, CSE researchers have created different scenarios, and say it is possible for the sector to stay close to the emission level of 2019-20, while achieving the production target of 2030.
CSE researchers analysed the production and emissions data of 10 cement companies that account for 70 per cent of the country’s total production. These are UltraTech Cement Limited, ACC Limited, Shree Cement, Ambuja Cement, Dalmia Cement (Bharat) Limited, Nuvoco Vistas Corporation Limited (previously known as Lafarge Cement), The Ramco Cements Limited, The India Cements Limited, JK Cement and Birla Corporation Limited. Of these, only five—Ultra-Tech Cement, ACC Limited, Shree Cement, Ambuja Cement and Dalmia Cement—are responsible for 51 per cent of the total emissions from the sector.
However, CSE researchers could find long-term emission data for only three of the 10 companies. These are UltraTech, Ambuja and ACC. An analysis of the data shows that between 2013-14 and 2021-22, CO2 emissions of Ambuja Cement have grown from 32 million tonnes to 62 million tonnes, while the emissions of Ambuja Cement and ACC Limited have grown only marginally—from 14 to 16.7 million tonnes and from 15.6 to 16 million tonnes, respectively. Further analysis shows that the emissions of these companies have a direct correlation with their production. For instance, CO2 emissions of UltraTech Cement have nearly doubled between 2013-14 and 2021-22, in tandem with its production that has increased to 90 million tonnes from 40 million during the eight years.
Surprisingly, CSE’s analysis shows that UltraTech Cement and Dalmia Cement, despite being among the top five emitters, have the lowest emission factors (the rate at which an activity releases GHGs into the atmosphere). Ramco Cements, which is the sixth major emitter among the 10 companies analysed, has the highest emission factor.
CSE researchers say that low emission factors indicate that companies in the country are making an attempt to reduce their carbon footprint by improving their energy efficiency and by replacing limestone with other raw materials like fly ash from power plant or slag from the steel industry.
Ordinary portland cement, which primarily uses limestone, has the highest emission intensity—a tonne of it produces 0.84 tonne of CO2. Industry sources say that till 1999, more than 70 per cent cement produced in the country was ordinary portland. But over the past two decades, companies have started replacing limestone with other raw materials to produce pozzolana portland cement, in which a certain portion of fly ash from power plants replaces limestone, and portland slag cement, in which some amount of slag from steel plants replaces limestone. These blended cement have low emission intensity. According to the 2022 report by Global Cement and Concrete Association (GCCA), an industry body, the emission intensity of pozzolana portland cement is 0.58 tCO2 per tonne of cement, and that of portland slag cement has the lowest 0.38 tCO2 (see ‘Composition matters’, p32). Today, blended cement account for 73 per cent of the cement produced in the country, notes the GCCA report. Pozzolana portland cement constitutes 65 per cent or the bulk of the cement manufactured, whereas ordinary portland cement and portland slag cement account for 27 per cent and 7 per cent of the production.
In February 2023, the Bureau of Indian Standards (BIS) has issued standards for a new cement variety called composite cement, which is a combination of limestone, fly ash, slag and gypsum. Its emission intensity is 0.41 tCO2 per tonne of cement. In this cement, industrial waste materials, fly ash and slag can constitute more than 60 per cent of the raw material, substituting limestone. A 2018 report by the World Business Council for Sustainable Development, an organisation of more than 200 international companies, says that for a cement plant with a capacity of 1 million tonnes per annum, production of composite cement requires 57 per cent less raw material, 52 per cent less thermal energy and 34 per cent less electrical energy when compared with the production of ordinary portland cement. But production of composite cement has not taken off yet and accounts for less than 1 per cent of total production in India, says the GCCA report.
As removing CO2 from limestone during calcination is highly emission-intensive, the more it can be substituted with other raw materials, higher will be the reduction achieved in the carbon intensity of cement. Furthermore, if this substitution is done with industrial waste materials like fly ash or slag, it is doubly beneficial, as these would have otherwise added to environmental pollution and contamination. But how will these remedies help reduce carbon emissions of the cement sector?
Based on industry analysis, CSE has projected three future emission scenarios for 2030:
Business-as-usual scenario: This is the scenario, where the cement sector continues on its growth trajectory of producing 660 million tonnes by 2030, without improving its CO2 emission factors and with the share of different types of cement produced remaining the same as it was in 2019-20. In this scenario, CO2 emissions are projected to grow almost at twice the levels of 2019-20.
Low-carbon pathway: The Indian cement industry has been innovative in its efforts to reduce emissions by improving energy-saving mechanisms and by increasing the use of alternative raw materials to substitute limestone. This has also increased the profitability of the industry. The existing policies of the government, which drive energy efficiency, put a carbon tax on coal and allow for the use of fly ash, among other strategies, have helped the industry reduce emission intensity by 44 per cent—to 0.67 tCO2 per tonne of cement in 2017 from 1.12 tCO2 per tonne cement in 1996. This translates into an annual 1.9 per cent decrease in emission intensity. For the low-carbon growth pathway scenario, this rate of decrease has been assumed to continue per year till 2030. And, CO2 emissions would show an increase of 1.6 times from the 2019-20 levels, or, compared to the business as usual scenario, a reduction of 77 million tonnes in CO2 by 2030.
Improved low-carbon pathway: Of the 10 cement producing companies studied by CSE, five have given clear targets for reducing CO2 in their annual or sustainability reports and on their websites. These five companies contributed almost 53 per cent of the total cement production in India in 2019-20, and aim to cut CO2 emissions by 10-25 per cent. Ambuja Cements, UltraTech Cement and ACC Limited, whose cumulative production was almost 132 million tonnes (nearly 40 per cent of the country’s total production) in 2019-20, have signed net-zero pledges for 2050. Signing a net-zero pledge means making an international commitment to UNFCCC to voluntarily reduce emissions by adopting science-based targets.
So, for this scenario, the production of the individual company has been assumed based on its future capacity declarations and current capacity utilisation. Similarly, the emission factors of the top five emitting companies have been calculated based on their 2030 targets (For 1 tonne of cement, UltraTech Cement’s 2030 emission factor is taken as 0.47 tCO2, ACC’s as 0.47 tCO2, Shree Cement’s as 0.55 tCO2, Ambuja Cement’s as 0.50 tCO2 and Dalmia Cement’s as 0.48 tCO2). All other cement-producing companies in the country are assumed to reach an emission factor of at least 0.49 tCO2 per tonne of cement, or an average of the top five emitting firms. The resultant projection in this scenario shows a CO2 reduction of almost 97 million tonnes compared to the business-as-usual scenario.
Apart from the three projected pathways, CSE has proposed an accelerated low-carbon pathway. This scenario suggests remedies that reduce carbon emission through different routes and is likely to result in a reduction of up to 174 million tonnes of CO2 emissions by 2030 compared to the business-as-usual scenario. Achieving this means emissions from the sector, if not less, will be closer to the levels seen currently—which is a drastic reduction from the business-as-usual scenario. This pathway involves implementation of a three-pronged strategy.
Increase share of blended cement: This strategy is based on minimising the use of limestone and increasing the share of other raw materials to substitute it. CSE proposes raising the share of blended cement in India’s total production by 2030, from the current 73 per cent to 90 per cent. For this, CSE has assumed that the share of ordinary portland cement would reduce to 10 per cent from the current 27 per cent; the share of pozzolana portland cement would increase from 65 per cent to 70 per cent; the share of portland slag cement would increase from 7 per cent to 10 per cent; and the share of composite cement to increase substantially from 1 per cent to 10 per cent in the total production in 2030. This change alone would reduce CO2 emissions to the tune of 43 million tonnes, or 10 per cent of the emissions in the business-as-usual scenario for 2030.
Increase share of recycled materials in production: The second strategy involves changing the composition of materials used in cement production. CSE suggests an increase in the upper limit of the amount of fly ash allowed in blended cement in India, specifically in pozzolana portland cement. BIS currently allows 15-35 per cent of fly ash mixing in pozzolana portland cement. CSE proposes to raise this cap to 45 per cent. Similarly, this scenario increases the average share of slag in portland slag cement from the current 57 per cent to 65 per cent. Although BIS allows up to 70 per cent slag usage for portland slag cement, its share does not cross 60 per cent. Similarly, for composite cement, while BIS allows a 50 per cent share for slag, the current average share in the country is 25 per cent. CSE proposes to increase this percentage to 30 per cent, along with the current 35 per cent share of fly ash. The 5 per cent increase is proposed keeping in mind the limited availability of blast furnace slag for cement production and the ongoing research on using different types of slag in cement without affecting quality.
CSE has calculated emission factors for all types of cement for this scenario based on the decrease in the share of clinker with increase in fly ash and slag. The scenario considers the same share of product mix as for 2019-20, and found that a reduction of 59 million tonnes of CO2 emission (almost 14 per cent) can be achieved compared to the business-as-usual scenario.
Increase use of non-fossil fuels: Fuels, mostly fossil ones, account for a large part of the cement sector’s CO2 emission. After changes in the mix and materials, CSE proposes substituting 50 per cent of the overall fuel requirement with alternative fuels like refuse-derived fuel (RDF), industrial waste and biomass by 2030. The resultant emission factors have been calculated by reducing 50 per cent CO2 emissions from the thermal energy requirement per tonne of cement for all types of cement. Compositions of different cements and their share of production have been considered the same as for 2019-20. This alone can bring a reduction of around 84 million tonnes of CO2, which is nearly 20 per cent reduction of emissions under the business-as-usual scenario.
Combine the three strategies: Now, what if the three actions are implemented simultaneously. In this scenario, blended cement will account for 90 per cent of the production, the share of recycled materials in pozzolana portland cement, portland slag cement and composite cement is increased, and 50 per cent of fossil fuel is replaced with alternative fuels. The combined scenario shows a reduction potential of 174 million tonnes, or 41 per cent, of CO2 emissions compared to the business-as-usual scenario for 2030.
It is clear that there are opportunities for reduced carbon intensity, even in this hard-to-decarbonise industrial sector. These options suggest various interventions that are possible in this decade (see ‘Choose ambitious pathways’). It may seem ambitious, but given the challenge of climate change and the existential threat it poses, we must move beyond the ordinary to the extraordinary and that business as usual must become unusual.
The cement sector belongs to a category of what is infamously referred to as the “hard-to-abate industrial sectors”. As the label suggests, emission reduction is a difficult exercise in these sectors, for they depend on fossil fuels to fulfil their requirement of high temperatures for processes or on raw materials that lead to GHG emissions during the manufacturing process. Ideally, India should change the production route for such sectors to enable deeper emission cuts, along with switching fuel. In some cases, such as the iron and steel sector, carbon capture, utilisation and storage (CCUS) may be necessary, particularly for blast furnace-basic oxygen furnace process in which substituting coal is difficult. A few big players like Steel Authority of India Limited (SAIL), Tata Steel (India) Limited, JSW Steel and Jindal Steel and Power are already implementing or planning to implement CCUS in their manufacturing plants. The option is to upscale the implementation of CCUS, and also explore ultra-low carbon-emission technologies in steel-making for their application and use in India.
But upscaling such technologies will require financing from the developed world. Without adequate financing, it is impossible for developing countries like India to make an accelerated transition towards cleaner production and increase production to fulfil its developmental needs. Domestic finance (public and private) may not be enough to make possible a timely transition; hence it is essential to explore options for international finance—but only on just conditions.
India already has a net-zero target to meet by 2070, but for the hard-to-abate sectors, short-term or interim targets also need to be set domestically and the government must put out clear decarbonisation pathways to meet these targets. The country needs an enabling policy framework for implementation of these pathways on the ground and for mobilising both domestic and international finance.
A look at the hard-to-abate sectors globally shows that China is the largest production hub, and is usually followed by India as the second or the third largest producer for different sectors. Even as China’s production is likely to plateau in the coming years, India’s production is set to go up in the coming decades. This makes India a crucial player in curbing GHG emissions from hard-to-abate sectors globally. Along with India, other developing economies will also see an increase in production levels and would need to overcome the challenges faced by the hard-to-abate sectors.
The developed world already has technological and financial resources to transition its hard-to-abate industries; it now needs to fulfil promises made to help developing countries do so. The key here will be for the developed world to extend support without adding to any financial or legal burden on developing countries.
This was first published as a cover story in the 1-15 August, 2023 print edition of Down To Earth